Ship launching airbags are to be constructed of a cylindrical body and two conical heads (one at each end). Ship launching airbags with lots of advantages, such as easy to operate, time saving, saving investment safety, etc.
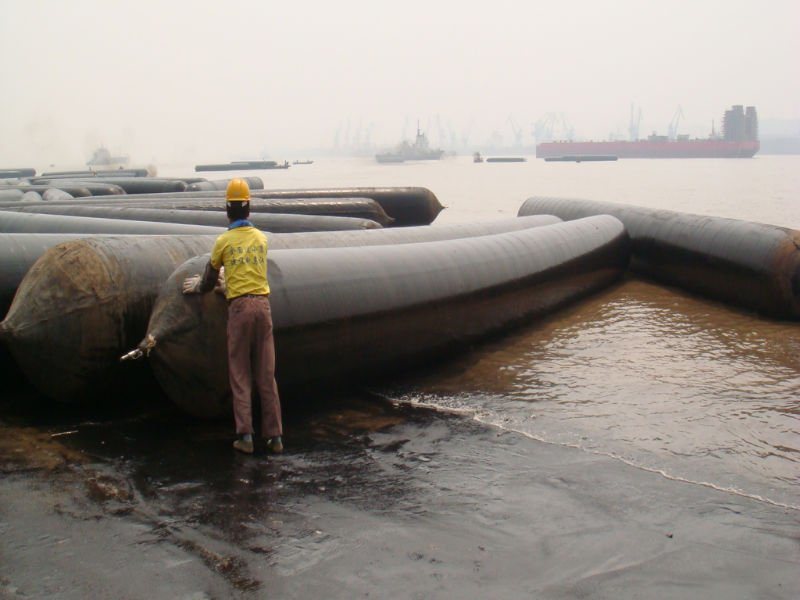
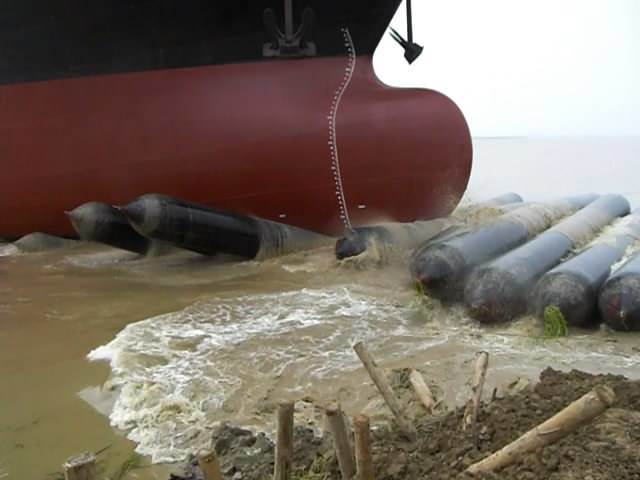
Major Strengths of Ship Launching Airbags:
High level of safety: Equipped with a reliable safety valve, our airbags can stand the maximum pressure up to 4 times that of the operating pressure.
Good air tightness: Pressure decreases less than 10% for a period of 24 hours.
Long lifespan: It is guaranteed that our airbags can sustain their designed operating pressure for 3 years.
Specification
1. Structure
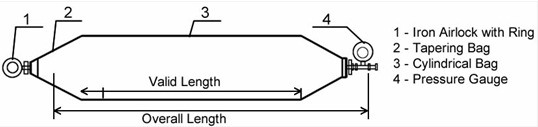
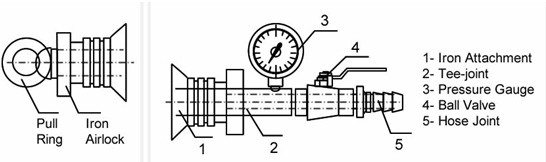
2. Diameters: 0.8 m - 2.0 m or customized.
3. Length: 6 m - 20 m or customized.
4. Loading Capacity: about 10 T/M to 40 T/M.
5. Grades:
Ordinary airbags - 3, 4 or 5 layers of synthetic-tire-cord.
High bearing capacity airbags - 6, 7 or 8 synthetic-tire-cord.
Super high bearing capacity airbags - 9, 10 or more layers of synthetic-tire-cord.
6. Accessories: Pull ring, iron airlock, tee joint, pressure gauge, ball valve, hose joint etc.
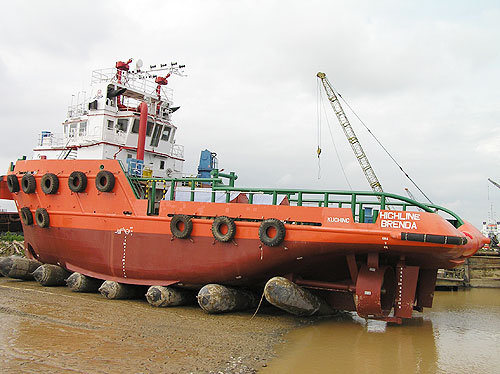
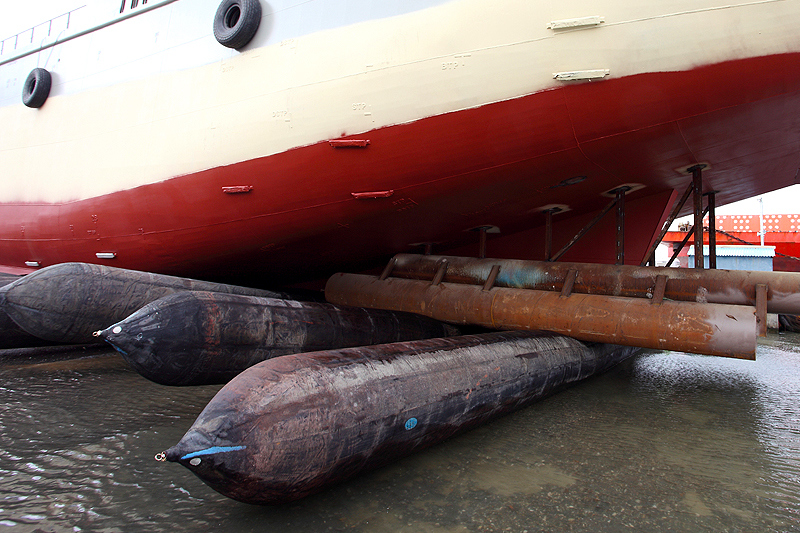
7. Technical Data of Ship Launching Airbags
Model | Diameter (m) |
Initial pressure (KPa) |
Rated working pressure, Pe (KPa) |
Bearing capacity (kN/m) | Minimum burst pressure (KPa) |
QP3 | 0.8 | 25 | 130 | 114 | 390 |
1.0 | 18 | 100 | 110 | 300 | |
1.2 | 15 | 85 | 112 | 260 | |
1.5 | 13 | 70 | 115 | 210 | |
QP4 | 0.8 | 35 | 170 | 149 | 510 |
1.0 | 25 | 130 | 143 | 390 | |
1.2 | 20 | 110 | 145 | 330 | |
1.5 | 16 | 90 | 148 | 270 | |
1.8 | 14 | 80 | 158 | 240 | |
QP5 | 0.8 | 48 | 210 | 184 | 630 |
1.0 | 35 | 170 | 186 | 510 | |
1.2 | 28 | 140 | 185 | 420 | |
1.5 | 20 | 110 | 181 | 330 | |
1.8 | 16 | 90 | 178 | 270 | |
QP6 | 1.0 | 45 | 200 | 219 | 600 |
1.2 | 32 | 165 | 217 | 490 | |
1.5 | 25 | 130 | 215 | 390 | |
1.8 | 20 | 110 | 218 | 330 | |
Note: 1. Rated working pressure:±5%. 2. Compress deformation: ±2%. 3. Bearing capacity: one meter airbag at a deformation rate of 70%, internal pressure equivalent to the rated pressure value of Pe. |
9. Rubber Material Test:
No. | Test item | Required value | Test method | |
1 | Tensile Strength, MPa | ≥ 18 | ISO37 | |
2 | Elongation at break, % | ≥ 400 | ISO37 | |
3 | Hardness, shore A | 60±10 | ISO7619-1 | |
4 | Tear Strength N/cm | ≥ 400 | ISO34-1 | |
5 | Compression set, % (70 ºC ± 1 ºC, 22 h) | ≤ 30 | ISO815-1 | |
6 | After thermal aging at (70 ºC, ±1 ºC, 96 h) |
Holding of pull lengthening,% | ≥ 80 | ISO188 |
7 | Holding of elongation at break,% | ≥ 80 | ISO188 | |
8 | Change of hardness, hardness | ≤ 8 | ISO7619-1 | |
9 | Static ozone aging at 40 ºC*96 h, {ozone concentration( 50±5)*10} |
No crack | ISO1431-1 |
10. Reinforcing Material: the warp should be (90±5) cord per 100 mm in width, and the breaking strength shall be more than 205 N per cord.
Â
11. Appearance: The appearance of an air bag shall be smooth, glossy and without blemish such as crack, blister, delamination pits or impurities.
Â
12. Dimensional Tolerances:
The length and diameter of an airbag shall be measured with the rated working pressure and be within ±3%.
Â
13. Ship Launching Airbags Performance:
D (M) |
(4-5 layers) | (6-8 layers) | Â | ||
Initial pressure (MPa) |
Working pressure (MPa) |
Initial pressure (MPa) |
Working pressure (MPa) |
 | |
 | |||||
1.0 | 0.14 - 0.16 | 0.12 - 0.14 | 0.22 - 0.26 | 0.20 - 0.24 | Â |
1.2 | 0.12 - 0.14 | 0.10 - 0.12 | 0.20 - 0.24 | 0.17 - 0.22 | Â |
1.5 | 0.10 - 0.12 | 0.08 - 0.10 | 0.15 - 0.20 | 0.13 - 0.18 | Â |
1.8 | 0.08 - 0.10 | 0.07 - 0.09 | 0.13 - 0.16 | 0.11 - 0.14 | Â |
2.0 | 0.07 - 0.09 | 0.06 - 0.08 | 0.12 - 0.15 | 0.10 - 0.13 | Â |
Â
Desulphurizing Deduster
Desulfurization Dust Collector is a professional desulfurization equipment for turbocharged turbulent dust removal and desulfurization technology.
introduce
The principle of the work is that the sulfur containing gas is subjected to a turbocharged turbulence device, with the state of high speed rotation and diffusion and the intensified turbulent mass transfer formed by the absorption slurry. The process of mass transfer is to make gas liquid form emulsion layer, not only chemical absorption and fast, but also close to neutral, so it can keep the whole process high and stable mass transfer rate. Therefore, it is a very excellent low resistance and high efficiency desulfurization equipment.
The company has turbocharged turbulent mass transfer desulfurization equipment technology, belonging to the third generation of high-tech products. Its technical core is: Based on the theory of permeable surface updating, based on the strong mass transfer mechanism of mixed turbulence, it belongs to the purpose of separating the dispersed dust particles, smoke and harmful gases from gas, air or waste gas by using liquid as a separation agent and purifying the dust from gas, air or exhaust gas, and has the high technology of dust removal and desulfurization at the same time. Characteristics are: dust removal and desulphurization integration, low energy consumption, small area, simple operation, high efficiency, low operating cost, no clogging, stable operation, low pressure resistance loss, suitable for various sulfur fixing agents (CaO, MgO, NaOH, CaCO3, Na2CO3, NH3, H2O, industrial waste alkaline solution) and other advantages. At home and abroad, the technology of wet dedusting and desulfurization is at the leading level. And in the application of coal-fired industrial boilers, the achievement of zero emissions is achieved.
The desulfurization equipment is used in the industry of desulfurization and dust removal in coal fired boiler. The dust removal and desulfurization equipment can be used widely. It can be wet and wet desulphurization, and it can also be integrated with dust removal and dust removal. It is not only suitable for dust removal and desulfurization of coal-fired circulating vulcanized bed boilers, but also can be applied to the wet desulphurization, dust removal and flue gas purification of coal fired chain boilers and two oxygen removal. The sulphur efficiency is high and the tail gas is cleaned thoroughly. It is used in the furnace industry to remove the hydrogen fluoride and the acid waste gas purification equipment of the kiln tail gas, and the desulphurization of the tail gas of pellets and sintering machines. The purification efficiency of desulfurizer is very high. The SO2 of the original flue gas is removed from 11000mg/m3 to below 120mg/m3. It is widely used in the pellet smoke field of steel mill. It is a low resistance and high efficiency wet dust removal and desulfurization equipment and a new desulfurization equipment environmental protection product. Dust remover is used to remove harmful dust in the gas phase. On this basis, the desulfurization effect is increased, that is, the desulphurization dust collector.
Desulphurizing dust collector is generally wet desulphurizing dust collector, wet desulphurization and dust removal has water membrane desulfurization and dust removal, impact water bath desulfurization and dust removal.
The advantages of wet dust removal are easy to maintain, and can be prepared by different dedusting agents, at the same time, the effect of dust removal and desulphurization (denitrification) is achieved; the disadvantage is that the dedusting liquid needs to be treated, which may lead to two pollution.
After years of improvement, various types of water film desulfurization and dust remover have been developed, such as hilly type, swirling plate type, swirl column type, floating ball type, sieve plate type, and so on. Equipment technology is becoming mature day by day, each has advantages and disadvantages, and enterprises can choose different types according to their own needs.
Working principle
Desulphurization is a technology to control sulfur dioxide emissions. The dust collector can not only remove sulfur dioxide from flue gas, but also produce high value-added sulphuric acid ammonia fertilizer products. The boiler dedusting equipment uses a certain concentration of ammonia water (28% as an example) as desulfurizer, and produces the sulphuric acid ammonia slurry which is transported to the chemical fertilizer plant treatment system. The ammonia demand in the desulfurization process is automatically adjusted by the preset PH control valve and measured by the flowmeter. The sulphuric acid ammonia crystals crystallized in saturated sulphuric acid ammonia slurry in the desulphurization dust collector to produce suspended particles with a weight ratio of about 35%. These serous quilts are pumped to the processing field, dehydrated through primary and two stages, and then sent to the chemical fertilizer plant for further dehydration, drying, condensation and storage. The boiler dust remover also generates a considerable by-product to achieve a definite economic benefit.
Desulphurizing Deduster,Desulphurization Deduster,Desulphurization And Denitrification Deduster,Desulphurizing Gas Purifier
Botou Youjian Environmental Protection Equipment Co. LTD. , http://www.btdustmachine.com