Custom enclosures are essential in many industries where specialized protection and housing for equipment is required. These enclosures are not just generic boxes—they are designed with precision to meet exact specifications. Whether it's for electronics, medical devices, or industrial machinery, custom enclosures ensure that your equipment remains safe, functional, and efficient. The value of custom enclosures lies in their ability to provide tailored solutions that off-the-shelf products often cannot match. By choosing a custom enclosure, businesses can enhance performance, extend equipment life, and improve operational efficiency. This makes them an investment in long-term reliability and success.What to Learn About Custom Enclosures in Metal Fabrication
- The importance and benefits of custom enclosures
- They offer protection and housing for sensitive equipment
- Customization options are tailored to specific industry needs
- Precision fabrication techniques and material choices
- Techniques like laser cutting, welding, and powder coating
- Materials such as aluminum, stainless steel, or galvanized steel
- How to choose the right fabrication partner
- Factors like experience, capabilities, lead times, and customer service
Types of Custom Enclosures
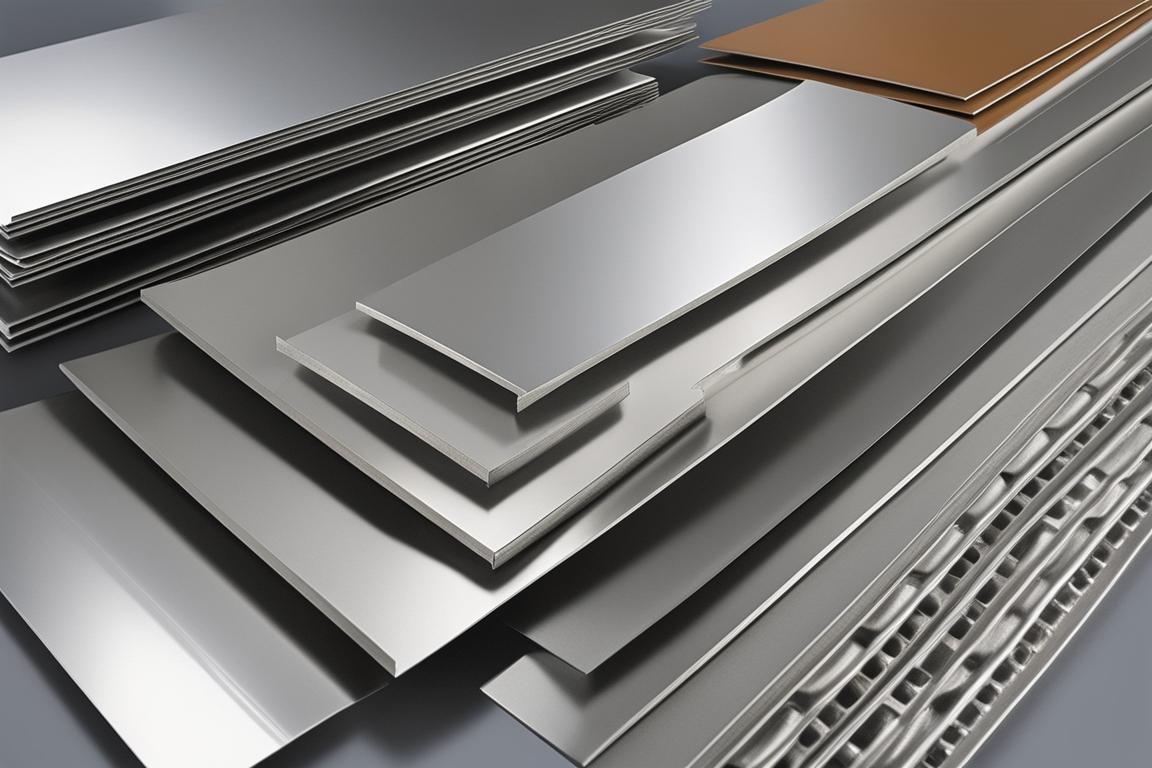
Materials Used in Custom Enclosures
Custom enclosures are made from a variety of materials, each chosen based on the environment and application. Aluminum is popular for its lightweight and durability. Stainless steel offers excellent corrosion resistance, while galvanized steel is ideal for harsh conditions. The choice of material directly impacts the strength, longevity, and suitability of the enclosure.
Varieties of Custom Enclosures
Enclosures come in many forms, including rackmount units for organized equipment storage, console enclosures for centralized control systems, and fully customized designs that fit unique requirements. These variations allow for seamless integration into any setup, ensuring both protection and accessibility.
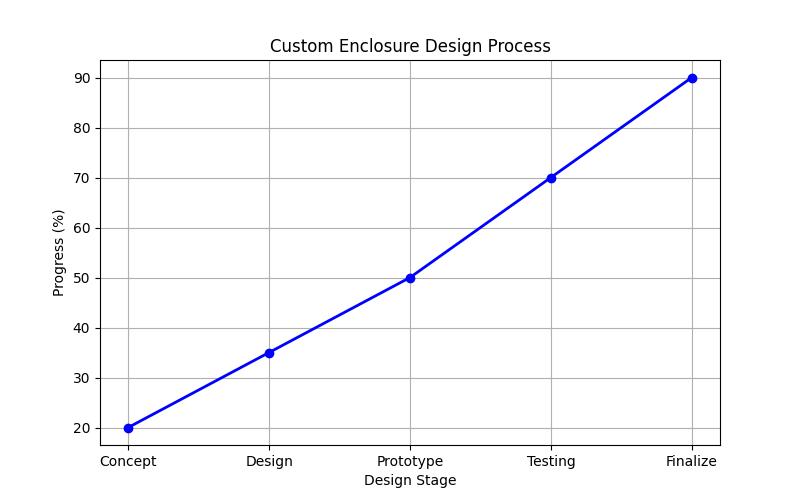
Design and Engineering of Custom Enclosures
The design process begins with detailed planning using CAD software to create 3D models. This allows engineers to test and refine the design before production. Every detail is considered, from structural integrity to ease of access, ensuring that the final product meets all functional and aesthetic requirements.
Precision Fabrication Techniques for Custom Enclosures
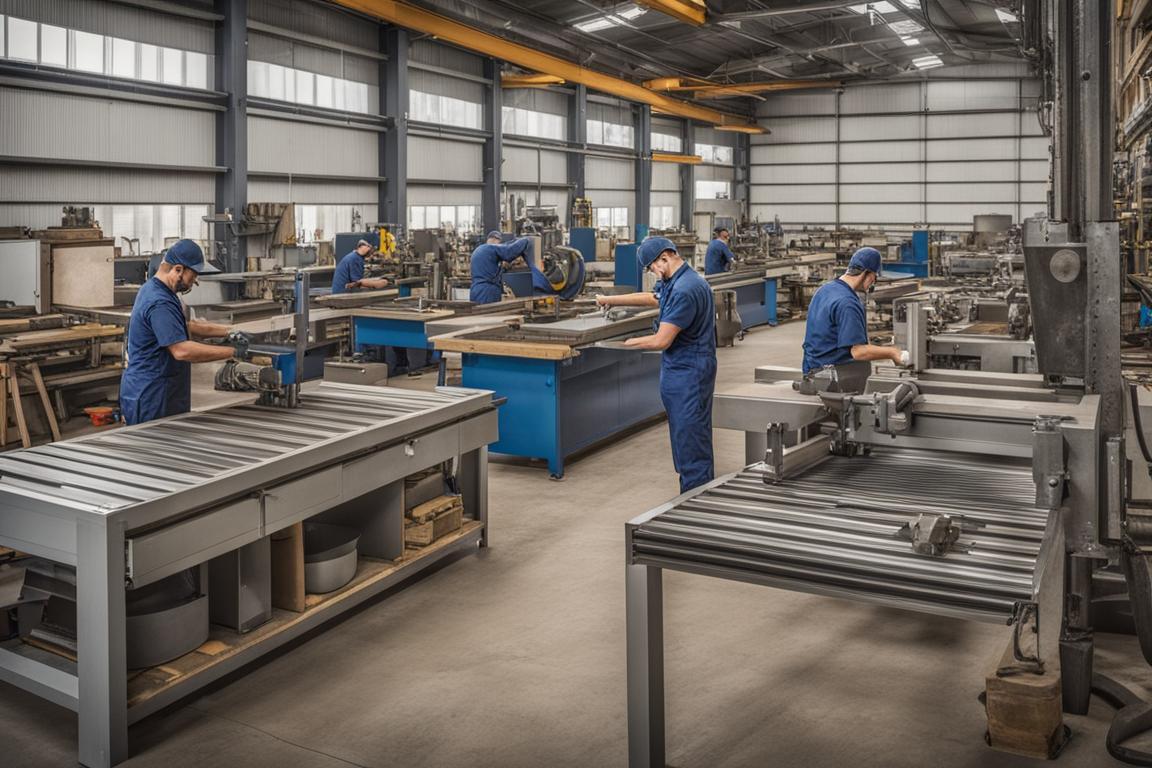
Fabrication Processes
Modern fabrication involves precise methods such as laser cutting, CNC punching, bending, welding, and powder coating. These techniques ensure that every component is manufactured with high accuracy and consistency, resulting in a durable and professional-looking enclosure.
Importance of Precision
Precision in fabrication is critical. Even the smallest error can affect functionality and safety. High-quality manufacturing ensures that the enclosure fits perfectly, functions as intended, and lasts for years without issues.
Customization Options for Enclosures
Tailored Features
Custom enclosures can be modified in many ways—sizes, ventilation, mounting options, door types, and finishes. These features allow for flexibility and adaptability, making the enclosure suitable for almost any application.
Industry-Specific Customization
Some enclosures are designed to meet specific standards, such as IP ratings for environmental protection or EMI/RFI shielding for electrical interference. This level of customization ensures that the enclosure performs optimally in its intended environment.
Quality Control and Testing Procedures
Ensuring Quality
Throughout the manufacturing process, strict quality checks are performed. From material selection to final assembly, every step is monitored to ensure that the enclosure meets high standards of performance and reliability.
Certifications and Standards
Certifications like ISO 9001:2015 indicate that a manufacturer follows rigorous quality management systems. Compliance with these standards ensures that the final product is consistent, reliable, and built to last.
Quality Control and Testing Procedures | Applications of Custom Enclosures |
---|---|
– Quality control measures ensure fabrication standards are met | – Telecommunications: safeguarding sensitive equipment |
– Compliance with industry standards like ISO 9001:2015 | – Electronics: organizing and protecting components |
– Rigorous testing procedures to guarantee reliability | – Healthcare: optimizing equipment performance |
– Inspections at various stages of production | – Aerospace: enhancing safety measures |
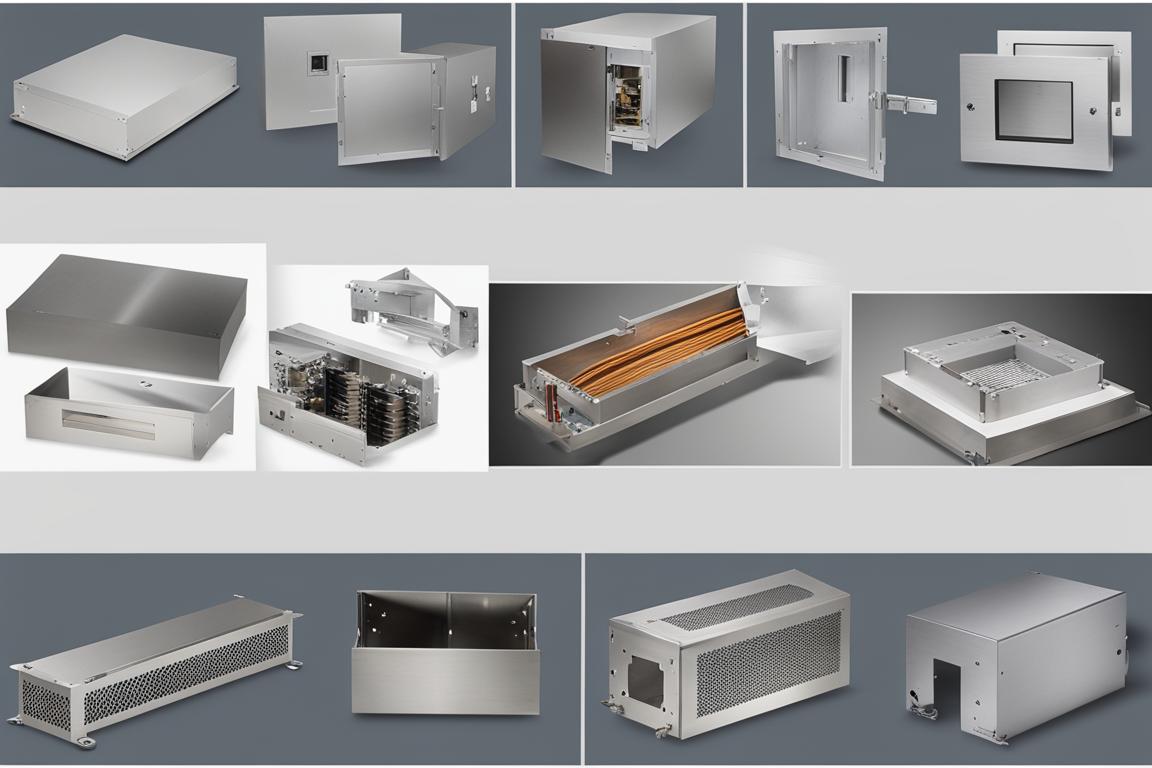
Applications of Custom Enclosures
Custom enclosures are used across a wide range of industries, from telecommunications and healthcare to aerospace and electronics. Their versatility allows them to protect, organize, and enhance the performance of equipment in any setting. Whether you're looking for a simple housing solution or a complex, engineered unit, custom enclosures can be tailored to suit your needs.
Case Studies on Custom Enclosures
Real-World Success Stories
Many companies have successfully used custom enclosures to solve real-world problems. These case studies demonstrate how tailored solutions can improve efficiency, reduce downtime, and increase safety. Investing in custom enclosures can lead to measurable improvements in your operations.
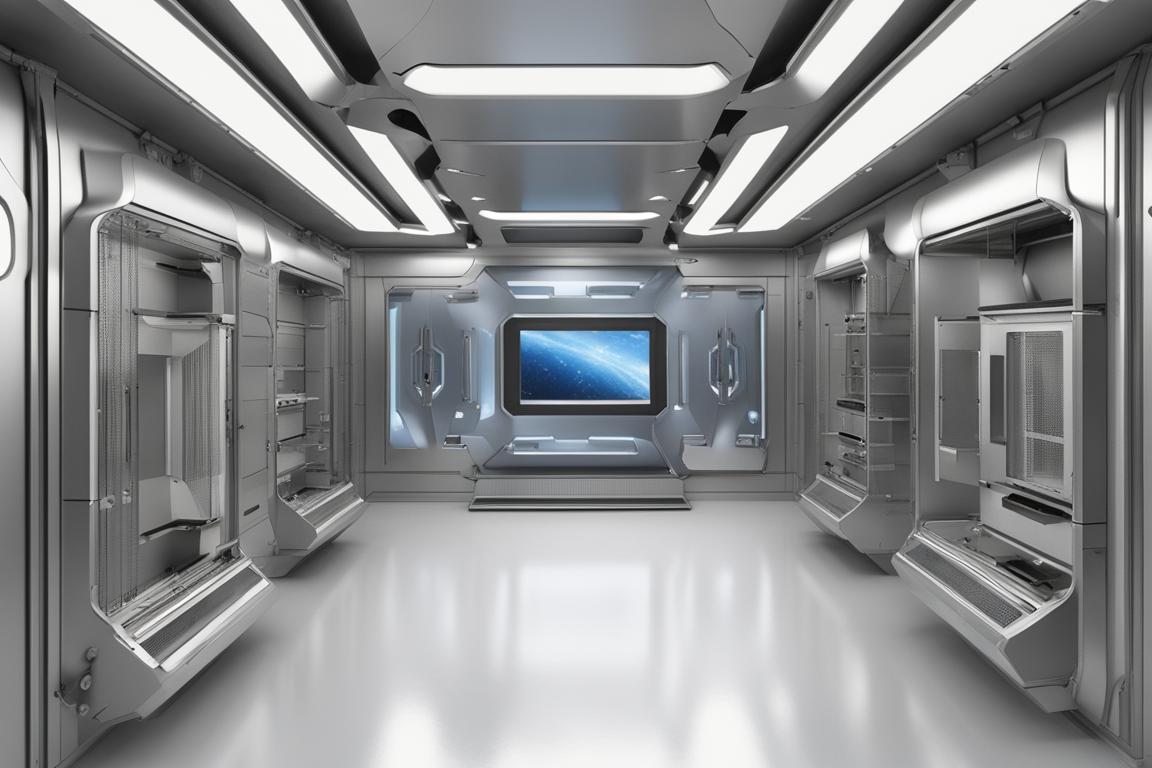
Future Trends in Custom Enclosures
Technological Advancements
The future of custom enclosures is being shaped by new technologies. Smart enclosures with remote monitoring, sustainable materials, and automated manufacturing processes are becoming more common. These innovations are helping manufacturers deliver better, faster, and more eco-friendly solutions.
Selecting a Fabrication Partner for Custom Enclosures
Choosing the Right Partner
Selecting the right fabrication partner is crucial. Look for a company with experience, strong capabilities, fast turnaround times, and excellent customer support. A reliable partner will help you achieve the best results, ensuring your custom enclosure meets all your expectations.
Conclusion
In summary, custom enclosures are vital in modern industrial applications. They offer precise, tailored solutions that standard enclosures cannot. With proper design, fabrication, and quality control, they ensure the safety, efficiency, and longevity of your equipment. Whether you're in tech, healthcare, or manufacturing, custom enclosures can make a big difference.
For innovative and reliable enclosure solutions, explore Protocase’s custom electronic enclosures. If you need expandable and stackable options, check out Custom Cages’ large reptile enclosures.
Contact us today for expert assistance in designing and manufacturing custom enclosures that fit your specific needs.
Questions and Answers
Who can benefit from custom enclosures in precision sheet metal fabrication?
Companies in industries like electronics, telecommunications, and medical devices.
What materials are typically used for custom enclosures in sheet metal fabrication?
Common materials include aluminum, stainless steel, and galvanized steel.
How are custom enclosures designed and manufactured in precision sheet metal fabrication?
They are designed using CAD software and then fabricated using cutting, bending, and welding techniques.
What makes custom enclosures from precision sheet metal fabrication more costly?
The customization and precision involved in the design and manufacturing process can lead to higher production costs.
How can I ensure that my custom enclosure meets industry standards and regulations?
Work with a reputable sheet metal fabrication company that has experience in your industry and adheres to quality standards.
{"@context":"https://schema.org","@type":"FAQPage","mainEntity":[{"@type": "Question", "name": "Who can benefit from custom enclosures in precision sheet metal fabrication?", "acceptedAnswer": {"@type": "Answer", "text": "Companies in industries like electronics, telecommunications, and medical devices."}}, {"@type": "Question", "name": "What materials are typically used for custom enclosures in sheet metal fabrication?", "acceptedAnswer": {"@type": "Answer", "text": "Common materials include aluminum, stainless steel, and galvanized steel."}}, {"@type": "Question", "name": "How are custom enclosures designed and manufactured in precision sheet metal fabrication?", "acceptedAnswer": {"@type": "Answer", "text": "They are designed using CAD software and then fabricated using cutting, bending, and welding techniques."}}, {"@type": "Question", "name": "What makes custom enclosures from precision sheet metal fabrication more costly?", "acceptedAnswer": {"@type": "Answer", "text": "The customization and precision involved in the design and manufacturing process can lead to higher production costs."}}, {"@type": "Question", "name": "How can I ensure that my custom enclosure meets industry standards and regulations?", "acceptedAnswer": {"@type": "Answer", "text": "Work with a reputable sheet metal fabrication company that has experience in your industry and adheres to quality standards."}}]}Non-Metal Expansion Fabric Joint,Rubber Expansion Joint,Fabric And Non-Metallic Expansion Joint,Silicone Rubber Expansion Joint
Taixing Yingxing Composite Material Co.,Ltd , https://www.ptfecnyx.com