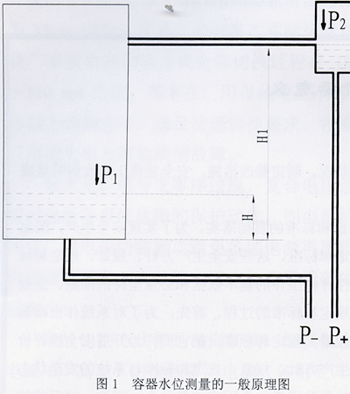
As shown in Figure 1, there are the following differential pressure calculation formulas:
â–³P=P+-P-=(P2+ÏH1g)-(P1+ÏHg)
Where ΔP is the differential pressure value measured by the differential pressure transmitter, Ï is the density of water at a certain temperature and pressure, g is the gravitational acceleration, and P1 and P2 are the space pressures on the negative pressure side and the positive pressure side, respectively, H For the actual water level in the container, H1 is the height of the reference water column.
After the container and its pipeline are formed, H1 is fixed and the P1 and P2 spaces are always connected, ie the space pressure is equal, so that the above differential pressure calculation formula can be transformed into:
P=Ïg(H1-H)
The ΔP can be measured by a differential pressure transmitter. Ï, g, and H1 are all known numbers. It is easy to calculate the H value, which is the actual water level of the container, using modern computer technology.
Second, the existing problem of the traditional measuring method of the condenser water level The condenser water level of the thermal power generating unit is an important parameter. The traditional condenser water level measurement shown in Figure 2, is generally designed and installed 2 sets of such water level measurement system, each set of water level measurement system includes two primary and negative pressure side sampling tube of the primary valve, from the water injection pipe (cited One injection valve from the condensate pump outlet, two secondary valves and one balance valve in the three-valve bank, two sewage discharge valves on the differential pressure transmitter, a total of eight manual valves, and two activities Connector.
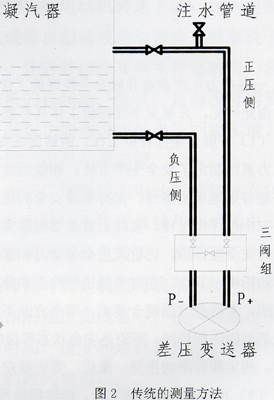
The two sets of water level measurement systems that are redundantly configured have a large deviation of 100-300 mm from each other, which is far from the actual water level indicated by the local glass water level gauge. The unit is particularly serious in the process of start-stop, centralized control room. The operating personnel cannot accurately monitor the water level of the condenser and affect the safe operation of the unit. Maintenance and repair personnel often maintain or eliminate the need for a long time, check the pressure transmitter, water injection, sewage, with solid oil or a variety of glue seal the joints of valves and joints, busy for a long time and finally aligned, and condensed steam When the vacuum of a device fluctuates, or if there is a big vibration in the sampling pipe, the previous work is abandoned.
Third, the cause analysis After the actual inspection and theoretical analysis, the above-mentioned traditional condenser water level measurement problems are mainly due to the following aspects:
3.1 Positive pressure side water seal influences water level measurement Condenser water level Positive pressure side sampling tube The sampling port is close to the condensing zone of the condenser. Under abnormal operating conditions, uncondensed steam will enter the horizontal section of the positive pressure sampling tube. Due to the small pipe diameter (D14×2 or D12×1) or dirt impurities in the pipe, the steam in the pipe does not flow back to the condenser after condensation, and a water seal is formed in the horizontal section, causing measurement deviations and slow change of the water level measurement point. .
3.2 System Leakage Impact Water Level Measurement Water injection pipe is introduced from the condensate pump outlet, the pressure is nearly 3MPa, as long as the water injection valve has a little internal leakage (small internal leakage is difficult to judge), additional positive pressure side pressure or full pressure side sampling tube In the horizontal section, the water level measurement will be significantly lower.
During the operation of the unit, the condenser is in a vacuum state, and the vacuum is more than -90 KPa. The traditional measurement system has 8 manual valves, and 2 joints, often need to discharge sewage or water injection, manually tighten the valve to screw, it is inevitable leakage, any valve or joint joint surface, even if it is a very weak leak, The impact on the water level measurement is great.
3.3 Vacuum fluctuations affecting the water level measurement Vacuum fluctuations have a certain influence on the positive pressure side water level. Vacuum rapidly increases in a short time, and the positive pressure side water level tends to decrease. If the pipeline leaks, the impact will be greater.
In addition, the loss of soda water in the thermal system and the thermal expansion of water can also affect the water level measurement.
Fourth, improve the method and effect shown in Figure 3, the sampling pipe diameter increased, replaced with D22 × 3 stainless steel pipe, a valve for D20, eliminating the possibility of water seal formation. The transmitter uses a differential pressure transmitter with a remote seal, eliminating the need for six valves and two unions. Two flanges are used to sense differential pressure from top to bottom. In this way, there is no need for frequent water injection, sewage disposal, and leakage prevention, which greatly reduces the workload of maintenance personnel.
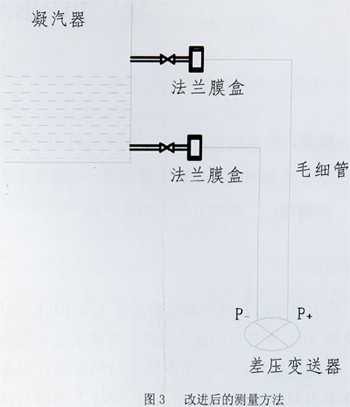
Practice has proved that the improved two sets of water level measurement systems have a mutual gap of less than 10mm, and the difference from the in-situ water level meter is less than 30mm at most, and they have been stable and reliable, meeting the condenser water level measurement technical requirements, and the effect is very good.
We have a complete plastic consumables production line. Mold-making, injection molding and sterilization, all the procedures are done efficiently in our own factory. Precision molds, high quality raw material and advanced equipment to produce and perform quality testing with strict and comprehensive rules to ensure our products meet the highest quality and performance standards expected by the hospitals, research institutions and industrial, clinical laboratories that we supply.
• Excellent mold-making ability.
Our R&D team, with over 30 years` experiences, work with high quality mold-making equipment imported from Germany and professional mold analysis software that allow NEST to develop more precise molds.
• Injection molding in Class 10,000 and Class 100,000 clean rooms, with strict quality control.
10,764 ft2 Class 10,000 clean room and 32292 ft2 Class 100,000 clean room, all-electric high-speed injection molding machines imported from Japan, raw material which meet USP Class VI requirements. Production and quality control are performed strictly in accordance with corresponding SOP.
• Sterilization by electronic beam irradiation.
The Rhodotron TT200 electron accelerator which imported from the IBA company, Belgium. A world leader in the E-Beam sterilization industry. Sterilization process has been certified by the ISO 11137 quality system. Compared with sterilization by cobalt 60 or ethylene oxide sterilization, sterilization by electronic beam irradiation is more efficient and safer. It requires less time and will not produce any chemical residue.
These non-treated polystyrene plates are transparent and DNase/RNase-Free. The bottom has a ridge allowing for easy handling and stacking. The plate has three vents for gas exchange.
L-Spreader
Using a grinding tool with high precision in combination with an ergonomic design, the efficient sterile L-Spreader specialized for Asian scientific researchers is developed and manufactured to effectively solve problems such as contamination or uneven application of spread plate in bio-labs, which helps to make domestic biological testing practitioners more efficient and simplify their tedious work during biological experiments.
Plastic Petri Dish,Laboratory Dish,Sterile Petri Dishes,Disposable Petri Dish
Wuxi NEST Biotechnology Co.,Ltd , https://www.nest-biotech.com