In recent years, with the rapid growth of the automotive industry, lead-acid batteries have experienced an explosive growth period. In 2010, China has become the largest lead battery producer in the world. However, at present, the lead storage battery industry still belongs to extensive development. There are too many enterprises and the scale is generally too small. There is a large number of low-level redundant construction. Due to the lack of relevant regulations and industry self-discipline, a large number of non-environmental protection facilities and non-qualified companies exist, and the pollution problem is particularly serious.
At present, the level of domestic lead-acid battery manufacturing companies varies greatly, both the most advanced production lines in the world and the most backward technologies that still use pure hand-workshops. According to statistics from the China Battery Industry Association, there are currently more than 2,000 lead battery companies in China, with about 1800 enterprises with production licenses, and only 200 companies with output value of over 5 million yuan, less than 10% of the total number. The output value is less than 100 million yuan.
For such a situation, rectification is imperative. In June 2011, the Lead-Acid Battery Branch of the China Electrical Equipment Industry Association was commissioned by the Ministry of Industry and Information Technology to begin drafting the Lead-Acid Battery Industry Access Requirements. The access conditions mainly focus on two aspects: First, to improve access thresholds for new projects, such as requiring new projects to adopt internal chemical processes, to enhance production process requirements, and to increase new production capacity, to replace the eliminated production capacity and market increment, and to control In the future, the productivity growth of the industry, etc.; the second is to eliminate outdated enterprises, and the existing enterprises in the industry are required to adopt advanced technologies such as automatic acid-mixing, automatic sub-board, brush-board, and automatic welding or automatic casting and welding within one year. Eliminating backward technology.
According to industry association statistics, in 2010 there were more than 2,000 domestic lead-acid battery companies, 10 companies with output value exceeding 2 billion yuan, and about 260 companies with more than 100 million yuan. At present, the investment of a fully automated plate assembly and assembly line is at least 100 million yuan. This standard means that more than 1,600 companies with an output value of less than one billion yuan in the industry are at risk of being eliminated.
The introduction of the conditions for entry was in line with market expectations. Along with the deepening of environmental protection in the lead-acid battery industry, it is expected that a large number of companies with technical backwardness will not be able to guarantee environmental protection requirements will be eliminated. The final industry resources will be concentrated in the hands of several leading companies. Helps improve the level of technology.
After the rectification of the lead-acid battery industry, the supply gap for electric vehicle batteries is the largest, about 40%, and the battery gap for automobile start-ups is also 20%. Due to the shortage of supply, the price of electric vehicle battery terminals has increased from RMB 400/group to RMB 700/group. With the further introduction of future access conditions, it is expected that the industry's supply gap will remain until mid-2012.
At the same time, the current market is extremely in short supply, the processing cost of one ton plate has increased from 4,200 yuan to 8,200 yuan. According to the material cost of 16,000 yuan for the current 1 ton plate, the cost of the plate has increased by nearly 20%. Companies that rely on outsourcing of plates to produce batteries face pressures to increase costs. Ultimately, the rising supply of prices will eventually lead to the price increase of terminal battery products. The sharp increase in the processing cost of the polar plate reflects the current situation in which demand exceeds supply. Enterprises with plate-to-plate assembly capacity can effectively avoid the impact of plate shortage and increase market share.
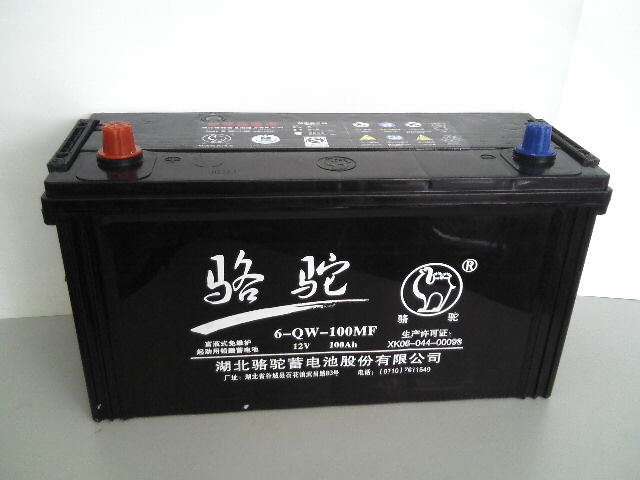
As the leading enterprises in the lead-acid battery industry are basically listed companies, these companies will usher in good development opportunities in the future. Among them, camel stock is a lead-acid battery leading enterprise in China, and its production capacity ranks first in China. The company raised funds to invest in 6 million KVAh annual output of new high-performance low-lead maintenance-free batteries, camel plastic products in Hubei Gucheng new construction projects and hybrid vehicle battery three projects.
Gucheng Camel Plastic Products Project is a car starter battery supporting project. After completion, it will add 10 million sets of battery tank cover annual production capacity, basically achieve the required total capacity of the future total production capacity of 1550KVAh; hybrid vehicle battery project will be new each year There are 1.44 million and 500,000 pieces of plate-type and pure lead thin-plate wound type valve-regulated lead-acid batteries. The project put into operation will help enhance the company's core competitiveness and reduce the risk of over concentration of the single business of automobile starter batteries.
PTFE Fabrics Self-Adhesive can be supplied as slitted tapes,and we name it as " PTFE Tape Adhesive".PTFE teflon adhesive tape provides an excellent release surface for a diversity of industrial applications requiring high temperature, electrical resistance, mechanical strength,and fire retardancy.Such as high temperature tape.
PTFE Adhesive Tape, PTFE Tape,High Temperature Tape
Jiangsu Zobon Conveyor Belt Co.,Limited , https://www.china-ptfefabric.com