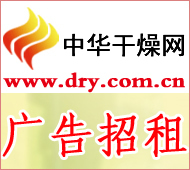
According to a research report released by the US consulting firm Frost & Sullivan in April, the global automotive carbon fiber composites market will grow to 7,885 tons in 2017, and the composite annual growth rate in 2010-2017 will reach 31.5%. At the same time, its sales will grow from $14.7 million in 2010 to $95.5 million in 2017. Although automotive carbon fiber composites are still in their infancy, they are driven by three factors and will usher in explosive growth in the future.
According to a study by Frost & Sullivan, from 2011 to 2017, the market's driving force for automotive carbon fiber composite materials mainly includes the following aspects:
First, due to the regulations of high fuel efficiency and low carbon emissions, the global demand for lightweight materials to replace metals is increasing, and carbon fiber composite materials have greater advantages than steel applications in automobiles.
Second, the prospects for the application of carbon fiber composites in automobiles can be expected. Many OEMs not only work with Tier 1 suppliers but also work with carbon fiber manufacturers to make available parts. Evonik has developed carbon fiber-reinforced plastic (CFRP) lightweight materials with Johnson Controls, Jacob Plastic, and Toho Tenax; the Royal Dutch Leica Turk (TenCate) and Toray of Japan The company reached a long-term supply agreement; Toray and Daimler reached a joint R&D agreement to develop CFRP parts for Mercedes-Benz. As demand increases, major carbon fiber manufacturers are stepping up research and development, and new breakthroughs will be made in carbon fiber composite material production technology.
Third, global auto demand will recover, especially in luxury and ultra-luxury car segments, which is the main target market for carbon composites. Most of these vehicles are produced only in Japan, Western Europe (Germany, Italy, the United Kingdom) and the United States. Due to the consideration of crashworthiness, style, and component assembly of automobiles, the foundry factories of automobiles will pay more and more attention to carbon fiber composite materials.
However, Frost & Sullivan also stated that the high price of carbon fiber, a considerable part of the cost depends on the price of crude oil, and is not expected to decline in the short term, which is not conducive to automakers to reduce costs. The foundry factory lacks overall engineering experience and has adapted to assembly lines based on metal components. Due to risk and replacement costs, it is very cautious about replacing equipment. In addition, people have new requirements for vehicle recyclability. According to the European Vehicle Reimbursement Law, by 2015, the recyclability of cars will increase from 80% to 85%. The competition between carbon fiber composites and mature reinforced glass composites will be even more intense.
Automotive carbon fiber composites are carbon fiber and resin composites used in a variety of structural or non-structural applications in automobiles. Compared with other materials, carbon fiber composites have higher tensile modulus and tensile strength. At the same time, carbon fiber composites are one of the materials with the lowest density. In the anti-crash structures, carbon fiber resin materials are the best choice. Resins used in combination with carbon fibers are most often epoxy resins. Polyesters, vinyl esters, polyamides, and polyetheretherketone are also used in small amounts.
Equipped with 10-inch Tubeless Tires which has long wear-resistance,features off-road tires, disc brake.
Electric Offroad Scooter,10 Inch Electric Scoote,Finance Electric Scooter,Scooter Electric Off Road
Yongkang Mysail Technology Co., Ltd. , https://www.mysail-scooter.com