The key to reducing emissions has important economic and social benefits.
1 Ordinary air compressor system exists. The current air compressor system has a very large starting current impact and cannot be started frequently. The main motor is often operated at no load, which is non-economical operation, and the power is wasted seriously; the main motor power frequency operation is empty. The noise of the press is very high; the impact of the main motor power frequency starting equipment is large, and the wear of the motor bearing is large, so the mechanical quantity is large when the equipment is maintained.
2Inverter air compressor system control scheme According to the existing air compressor operating conditions and combined with the production process requirements, the variable frequency air compressor system can meet the following requirements: The motor frequency conversion operation state keeps the gas tank outlet pressure stable and the pressure fluctuation range Control at ±0.02.
Under the power frequency operation mode, the pressure of the pressure storage tank obtained by the volume control of the air compressor and the control of the rebound and rebound pressure is still relatively rough and often fluctuates. This will affect the use of the end user, 3 and use the variable frequency air compressor to change the running speed, because the air compressor automation in the field of energy-saving renovation and environmental protection.
The air supply can be controlled smoothly, the pressure fluctuation control is more precise, and the end user can get a more stable air pressure.
The system has two sets of control loops, open loop and closed loop.
The inverter air compressor control system has two open-loop and closed-loop control modes. In the normal state, the closed loop control mode can be utilized, and the system will automatically control the operating speed of the air compressor according to the pressure of the compressed air in the pressure storage tank, thereby controlling the air supply volume of the air compressor. When the system is faulty or the pressure sensor is faulty, it can be switched to the open loop operation, and the operating speed of the air compressor can be directly given, so that the air compressor can be manually controlled to control multiple air compressor units. Switching.
The system only needs to be equipped with a frequency conversion air compressor, which can be used in multiple air compressors of the variable frequency system. In this way, when the air compressor needs to be repaired or replaced, it can be easily switched to another air compressor to operate in frequency conversion.
In order to ensure the energy saving effect of the air compressor, avoid the tolerance control as much as possible.
Because the tolerance control is very energy intensive, the use of variable frequency operation can save energy. When the air compressor is running at a variable frequency, the air compressor is prevented from entering the tolerance function through the electromagnetic valve; if the air compressor is operated at a power frequency, and the other air compressor is operated at a variable frequency, the pressure setting pressure of the air compressor operating at the power frequency is set. Improve and avoid tolerance operation.
Reliable switching.
The frequency conversion system simultaneously controls the frequency conversion and power frequency operation of multiple air compressors. Therefore, it is necessary to automatically start or stop the air compressor used by the power frequency according to the amount of compressed external air used. In order to ensure reliable judgment and switch air compressor operation, the system sets three hysteresis control to ensure reliable switching and prevent repeated switching failures.
3 air compressor frequency conversion control 3.1 frequency conversion control system air compressor constant pressure air supply intelligent control system is composed of inverter pressure sensor 7 control unit host computer software control unit. The control system prolongs the service life of the compressor while accurately controlling the outlet pressure of the air compressor according to the working state of the air compressor outlet machine detected by the pressure sensor, and greatly saves energy. Its characteristic is that the system control is more flexible, can provide a good setting monitoring interface, and has strong operability. The use of the column and the upper computer greatly improves the overall control level of the system, ensures the reliability and safety of the control, and further improves the protection of the system fault; in addition, the corresponding control display can be omitted, and the operation is convenient.
In order to avoid the tolerance control, a solenoid valve is installed in the steam source part of the volume control system, and according to the selection of the frequency conversion operation and the operating state of the system, it is automatically judged whether the tolerance is cut into operation.
The system passes, collects the pressure in the pressure tank, and the output pressure of the unit, and automatically controls the amount of gas supplied to the inverter through calculation.
Designed system principle box 1.
3.2 The control system between the air compressor units is not only to control the speed of the air compressor, but also to control the automatic operation of the power frequency standby air compressor according to the size of the external air pressure and the amount of gas used. When the amount of air used by the outside increases, the system will automatically increase the frequency. When the frequency reaches the maximum and the pressure is still not met, the system will automatically delay the start of another power frequency air compressor while still operating at constant pressure. When the external air consumption decreases, the system will automatically reduce the frequency. When the frequency reaches the minimum, the pressure is still too high, the system will delay the power frequency operation of the air compressor, and the air compressor of the variable frequency operation will still operate at constant pressure.
3.3 Features The power frequency conversion interlocking structure of the power supply end is adopted.
Direct power frequency and frequency conversion interlocking at the input power end of the motor ensure the safe operation of the system.
The use of large inertia, control algorithm, to achieve pressure without static control.
The compressed air output from the air compressor system first enters the gas storage tank, which can store the energy of the air pressure, so that the pressure changes smoothly, 3 but the existence of the gas storage tank will greatly increase the inertia of the system feedback, making the system become large. Inertia control system. The use of ordinary 0 control in a large inertia control system will likely lead to a series of ills such as system overshoot and severe oscillation amplitude and system instability. Therefore, in this program, a special large inertia and control system are adopted, which greatly reduces the occurrence of system overshoot and enhances the stability of the system.
With intelligent control, time-phase pressure control can be achieved.
The system can realize intelligent control according to the customer's requirements, that is, the time-phase control. The pressure setting of the system is no longer a simple set value, but a pressure curve set according to the daily gas consumption of the plant. After the pressure curve is determined, The system will automatically run according to the preset real-time clock according to the preset pressure curve.
The system can automatically divide the day 24h into multiple segments and up to 5 segments. The start time and end time of each segment can be set manually, and each segment can set a pressure value. In this way, in the low-peak period of the time domain gas, it can be operated at a lower pressure; on the contrary, in the peak period of the gas phase in the time domain, it can be operated at a higher pressure, and energy saving is possible as much as possible.
Complete security protection.
Zero-gas volume automatic shutdown function.
The system can also realize the automatic shutdown function of zero gas consumption according to the requirements of the user. That is, the air compressor outlet valve is an automatic check valve. When the gas consumption is relatively small and the pressure inside the gas storage pipe is very large, it can be automatically shut down, and then restarted when the gas consumption is relatively large. In this way, during abnormal working days such as holidays and weekends, or late at night, the system will automatically stop, so that the maximum energy-saving air compressor can be started after the inverter is used. Because the impact of the system will be, the air compressor can be started frequently. .
The upper computer interface is characterized by simpler settings and more intuitive monitoring.
The alarm signal is displayed in full Chinese, which is convenient and intuitive. You can determine where the fault is located in the first time and troubleshoot it. In addition, at the same time of alarm control, it also has a fixed sound and light alarm signal, and a help interface equipped with troubleshooting on the upper computer interface, which accelerates the response speed of the system failure.
In the upper computer interface, similar to the paperless recorder line acquisition and recording, the historical curve is automatically formed inside the human-machine interface, and the curve can be browsed in real time. 3 Key parameters are directly set in the upper computer interface.
If time-divided pressure control is used, the system will display the curve in a shape, which can be set directly on the curve. The key parameters can be divided into three levels of passwords to ensure the security of parameter settings.
4 Effect Analysis 4.1 Save the power outlet valve release valve is completely closed, cancel the air outlet release valve to adjust the air supply mode to avoid the resulting waste of electrical energy. The frequency of the motor is adjusted by the frequency converter to adjust the gas flow rate, so that the output power of the motor is basically proportional to the flow demand, and the motor is always operated with high efficiency to achieve a significant power saving effect. For example, when the gas consumption is the rated gas supply amount. At 50 o'clock, the power saving rate can reach more than 40. The energy saved can be divided into the no-load loss of two partial motors, that is, the current loss when the motor is unloaded, including the secondary loss, the loss of mechanical loss, etc., because the motor speed drops, and the current also drops, so its current The no-load loss is also greatly reduced; the output power is saved, the energy saving of this part is closely related to the supply pressure, and the frequency conversion control is adopted, which eliminates the pressure fluctuation caused by the original tolerance control and the frequent pressure fluctuations, etc., and the progress is stable. The supply pressure of the system reduces the load output power of the air compressor. Since the motor runs in a high efficiency state, the power factor is high, the reactive power loss is reduced, and a large amount of electric energy is saved.
Although the air compressor in the original system originally has its own pressure regulation function tolerance control, when the pressure is large, the system can automatically close the intake valve, which can often achieve the purpose of energy conservation, but not completely.
The no-load loss of the mechanical friction motor still exists. The high-pressure high-speed gas will bring a very large energy loss when flowing through the trapping valve. The frequency control can be used to cancel the valve control, which can save the energy consumed in this part.
4.2 Reduce equipment wear The first important reason for using the frequency conversion system is to reduce equipment loss, keep the equipment running smoothly, and extend the service life of the equipment.
The original air compressor can automatically adjust the opening degree of the intake and deflation valves according to the pressure. Therefore, when the margin is selected to be large, the valve may move frequently, which often causes the operating loss of the system to increase, even in the air pressure. Large time will cause the air compressor to stop automatically. The power frequency starting mode adopted by the inverter has not been increased. The impact of stopping and starting is very large. Most of the unit faults occur in the process of starting and stopping. 13 After the frequency conversion control system is added, the stepless speed regulation can be realized. The power level of the demand automatically adjusts the output of the air compressor, the valve action of the air compressor is significantly reduced, and there is no frequent shutdown phenomenon. The operation of the system is stable. 13 Wu Zhongzhi, Wu Jialin. Inverter application manual. Beijing Machinery Industry Press, 2002 Zhang Xuanzheng, Zhang Jinyuan. The application technology and practice of the inverter is called Beijing China Electric Power Press. In 2009, the 45th page of the power factor is analyzed.
Before the transformation, there is no flow meter in the pump outlet. No on-site and central control can realize accurate control of displacement through the mass flow meter method, accurately control the pump outlet pressure of the pump. 3, the differential pressure before and after the pump outlet valve Large, severe throttling, frequent internal leakage, affecting the daily maintenance and maintenance of the pump. The outlet pressure of the pump is only 1.3 rivers. Below, the pump outlet valve is frequently leaked. The number of operations is 25 to 3, about 20, and requires double pumping. The demand for external transportation has realized 7 lines of crude oil for external pumping, no standby pump, storage, safety hazards have been eliminated, and there is no need to upgrade the new pump or another reserve pump in the case of major safety hazards. The motor current is reduced to 80%, the power consumption per ton of oil consumption is 2.95kW.h, the fuel consumption is only about lkW.h, and the energy-saving effect is high. The fruit is significantly salty. The surface temperature of the motor is about 80, due to the temperature. High, the pump body is easy to salt and need to be cleaned regularly with clean water. The working child is big, and the temperature of the pump motor is very easy to damage. The temperature of the pump motor is about 651, the temperature drops sharply, and no salt formation occurs. So far, no failure has occurred in the pump. After completion, it can save about 390,000 degrees The cost of saving the new spare pump or the reserve reserve pump is at least 300,000 yuan, excluding the post-maintenance maintenance fee of the pump.
6 Conclusion Through the reform test of low-frequency external transmission of condensate outside the condensate, the main experience is that all the inverters can adjust the motor frequency and motor speed according to the working conditions under the specified conditions to meet the production requirements of the process and realize the festival. Electricity saving.
For the pump equipment, including the centrifugal pump or the volume pump, the inverter can reduce the head to increase the displacement or reduce the pump efficiency to reduce the pump consumption, and ensure that the pump is not easily damaged.
For the inverter with motor belts such as air coolers, the operating load of the air cooler can be adjusted by adjusting the frequency of the inverter, instead of adjusting the air cooler outlet baffle to adjust the operating parameters of the air cooler, which is simple in operation and energy-saving. .
Hebei Jimeng Highstrength Flange-tubes Group Co.,Ltd. is a large manufacturer engaged in producing all kinds of Forged Steel Flange with high quality and competitive price.
1.Standard |
ASME B16.5,ASME B 16.47,DIN EN 1092-1,DIN 1759-1,MSS SP-44,API605,GB/T9112 GB/T13402 HG/T20592 HG/T20615 ,GB/T 10746,GB/T10747 |
2.Material |
A105,Q235B,10#,20#,16Mn,45#,Q345B,304,304L316,316L |
3.Type |
Slip-On, Welding Neck, Blind, Socket Welding |
4.Size |
OD:1/2''--80'' |
5.Pressure Class |
CL: Class 150, 300, 600, 900, 1500 and2500. PN:PN 6, PN 10 , PN 16, PN 25, PN 40 and PN 64. |
6.Surface Treatment |
RF,FF,G,RJ,FF |
7.Packing |
wooden cases,wooden pallet,container or as your request |
8.Delivery Time |
within 20 days |
9. Usage |
chemical industry, electric power,oil pipe system,building,water transmission and so on. |
10.MOQ |
2MT |

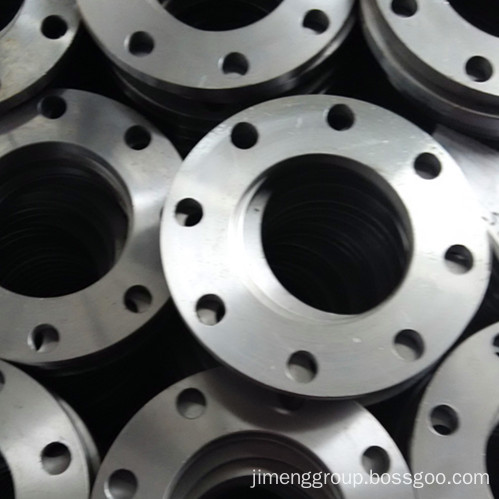
Class 300 Lap Joint Flange, ANSI 300 Flange, Forged Lap Joint Flange
Hebei Jimeng Highstrength Flange-tubes Group Co.,Ltd. , https://www.jimengflange.com